The Industrial Tape Market: UV Acrylic Adhesive vs. Solvent Acrylic Adhesive
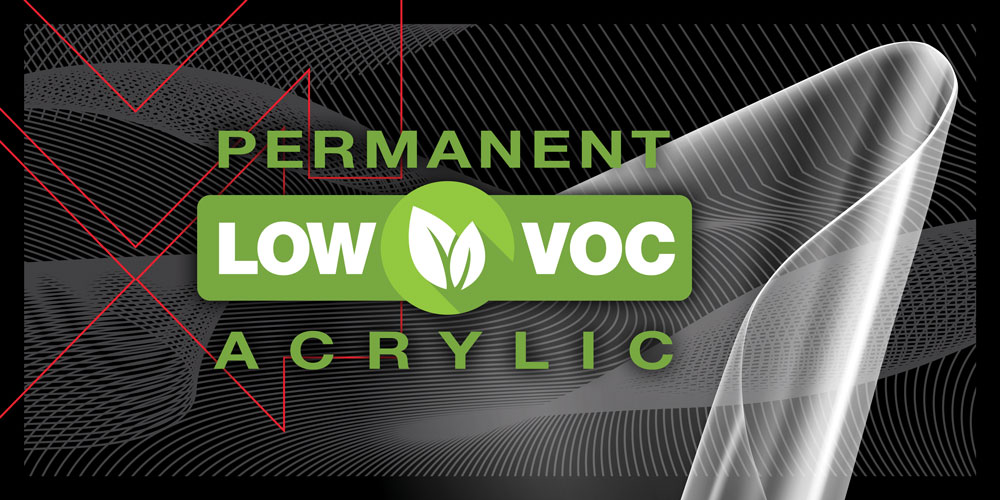
In the fast-evolving industrial tape market, the choice of adhesive plays a crucial role in determining the performance, durability, and environmental impact of the final product. Among the various types of adhesives available, UV acrylic adhesive and solvent acrylic adhesive are two prominent options. This blog post will explore the benefits of choosing UV acrylic adhesive over solvent acrylic adhesive and highlight why UV acrylic adhesive is becoming the preferred choice for many industries.
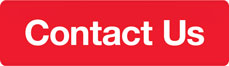
Environmental Impact
One of the most significant advantages of UV acrylic adhesive is its environmental friendliness. Solvent acrylic adhesives contain volatile organic compounds (VOCs) that can be harmful to both the environment and human health. These VOCs contribute to air pollution and can cause respiratory problems and other health issues. In contrast, UV acrylic adhesives are typically free from VOCs, making them a safer and more eco-friendly option. By choosing UV acrylic adhesives, companies can reduce their carbon footprint and contribute to a healthier environment.
Curing Speed and Efficiency
UV acrylic adhesives cure quickly when exposed to ultraviolet light, allowing for rapid bonding and processing. This fast curing time can significantly enhance production efficiency by reducing downtime and increasing throughput. In contrast, solvent acrylic adhesives often require longer drying times and may need additional equipment to facilitate the curing process. The quick-curing nature of UV acrylic adhesives makes them ideal for high-speed production lines and time-sensitive applications.
Superior Bond Strength and Durability
UV acrylic adhesives are known for their exceptional bond strength and durability. They provide excellent adhesion to a wide range of substrates, including metals, plastics, glass, and composites. This versatility makes UV acrylic adhesives suitable for various industrial applications, from automotive and aerospace to electronics and medical devices. Additionally, UV acrylic adhesives offer superior resistance to temperature fluctuations, moisture, and chemicals, ensuring long-lasting performance even in harsh environments.
Precision and Control
Adjusting the intensity and duration of UV light exposure can precisely control the curing process of UV acrylic adhesives. This level of control allows manufacturers to achieve consistent and reliable bonding results, reducing the risk of defects and improving overall product quality. On the other hand, solvent acrylic adhesives can be more challenging to control, leading to variability in bond strength and performance. UV acrylic adhesives' precision is especially useful in applications that call for high reliability and accuracy.
Health and Safety
Using UV acrylic adhesives can enhance workplace safety by minimizing exposure to harmful chemicals. Since these adhesives do not contain solvents, there is no risk of inhalation or skin contact with toxic substances. This can lead to a healthier work environment and reduce the need for costly safety measures, such as specialized ventilation systems and protective equipment. In comparison, solvent acrylic adhesives pose significant health risks to workers, necessitating stringent safety protocols and potential regulatory compliance issues.
Cost-Effectiveness
While the initial cost of UV curing equipment may be higher than that of solvent-based systems, the long-term benefits often outweigh the upfront investment. UV acrylic adhesives can reduce production time, increase throughput, and minimize defects, leading to overall cost savings. Additionally, the reduced need for safety measures and environmental compliance associated with UV acrylic adhesives can further lower operational costs. Companies that prioritize efficiency and sustainability may find UV acrylic adhesives to be a more cost-effective choice in the long run.
Solvent Acrylic Advantages
Despite the numerous advantages of UV acrylic adhesives, solvent acrylic adhesives still hold certain benefits that can make them a better choice in some scenarios. Solvent acrylic adhesives often offer superior adhesion to certain substrates, especially those that are difficult to bond, such as oily or contaminated surfaces. They also tend to provide better initial tack, which can be crucial in applications where immediate handling strength is required. Additionally, solvent acrylic adhesives can withstand higher temperatures better than UV acrylic adhesives, making them suitable for applications involving extreme heat. These factors can make solvent-based acrylic adhesives a more suitable option for specific industrial needs.
Conclusion
In the industrial tape market, the choice between UV acrylic adhesive and solvent acrylic adhesive can have a significant impact on production efficiency, product performance, and environmental sustainability. UV acrylic adhesives offer numerous advantages, including environmental friendliness, fast curing times, superior bond strength, precision control, enhanced health and safety, and long-term cost-effectiveness. As industries continue to prioritize sustainability and efficiency, UV acrylic adhesives are poised to become the adhesive of choice for a wide range of applications.
By embracing UV acrylic adhesives, companies can not only improve their production processes and product quality but also contribute to a greener and safer world. The shift towards UV acrylic adhesives is a testament to the growing awareness of the importance of sustainable practices in the industrial sector.
Magnum Tapes & Films has the experience to create custom solutions, too. When you need quality PSA tape that meets your specifications, contact the Magnum Tapes & Films team to discuss your needs and our solutions.
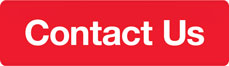